¿Qué tan bien conoces los protocolos de bloqueo y etiquetado? En este artículo hablaremos sobre las opciones para mejorar la seguridad eléctrica en tu empresa.
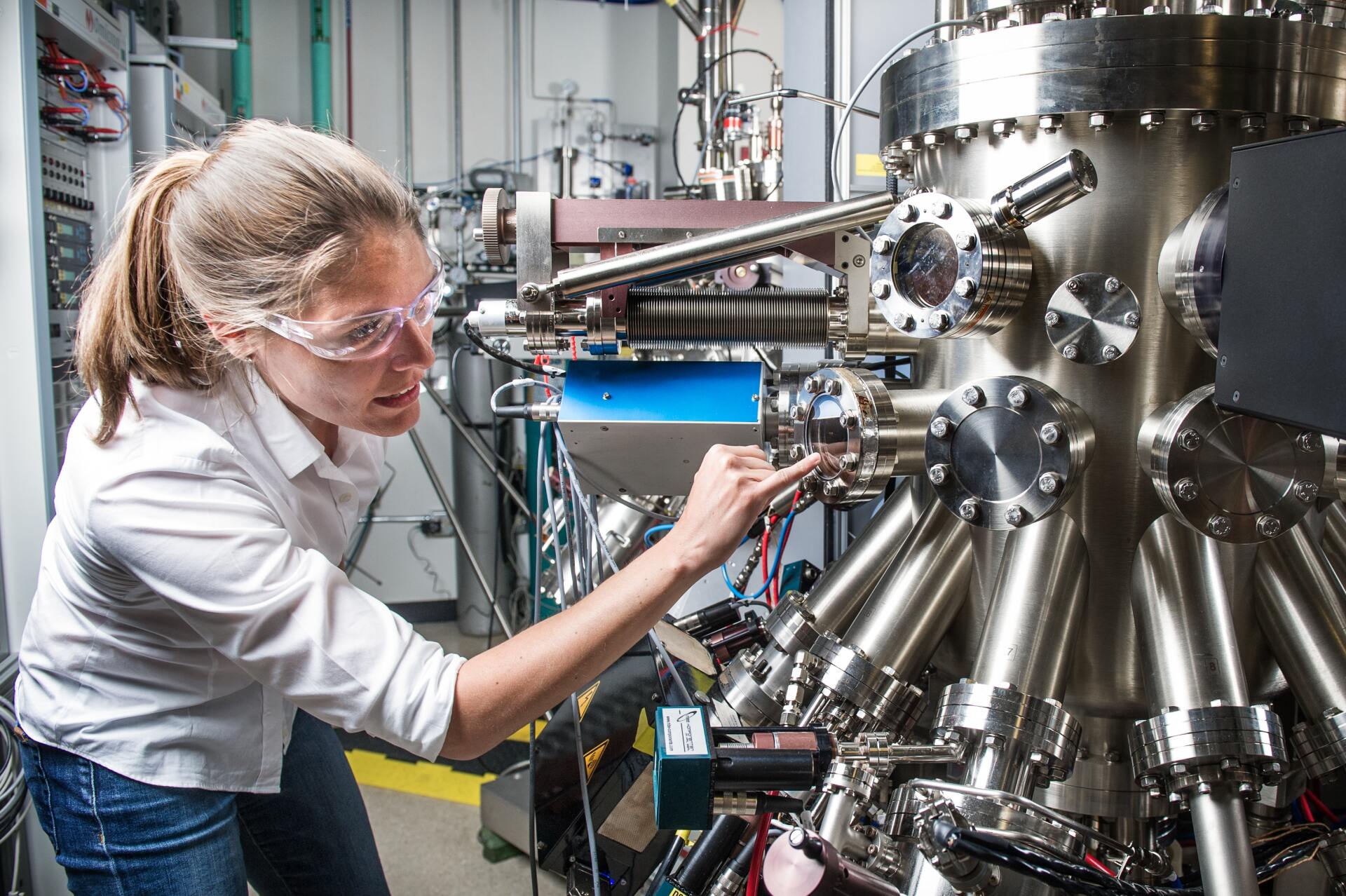
El control de las energías peligrosas, llamado también LOTO (Lock Out Tag Out), tiene como finalidad evitar que las energías que utilizan las máquinas e instalaciones puedan dañar a los trabajadores durante las intervenciones que realizan para su mantenimiento y servicio.
En parámetros normativos, la Administración de Seguridad y Salud Ocupacional (Occupational Safety and Health Administration, OSHA por sus siglas en inglés) establece reglas que describen los métodos que deben utilizar los empleadores para proteger a sus empleados contra peligros.
Hay cuatro grupos de normas OSHA: industria general, construcción, industria marítima y agricultura.
Específicamente relacionado con la seguridad eléctrica, el Bloqueo y Etiquetado es una norma de OSHA que protege a los trabajadores al desenergizar circuitos eléctricos, válvulas de cierre, neutralizar temperaturas extremas y asegurar partes móviles con el fin de que la energía peligrosa no sea reactivada mientras se da servicio de mantenimiento al equipo.
Seguridad eléctrica en el procesamiento de alimentos
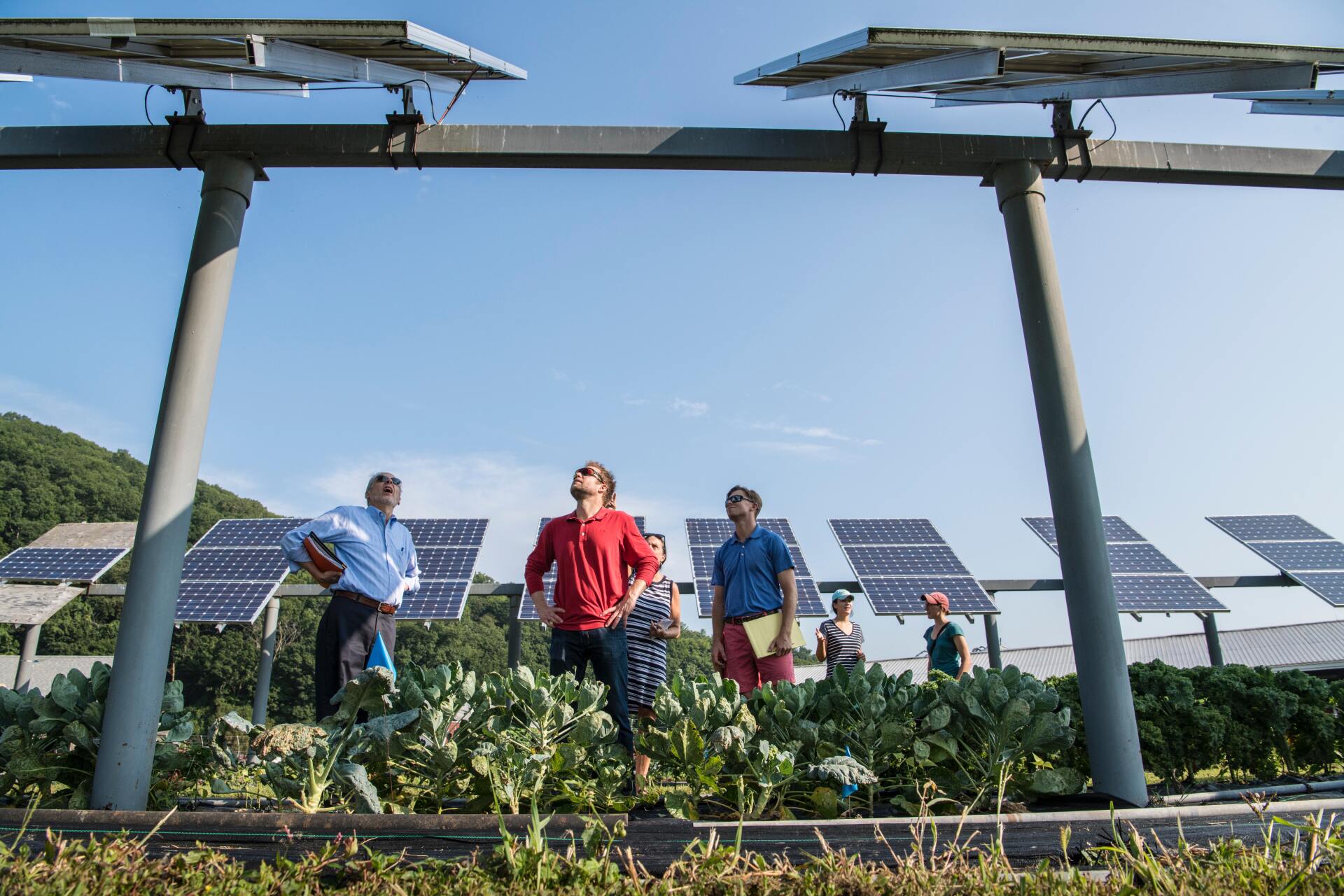
El bloqueo y etiquetado de equipo eléctrico, es un procedimiento de seguridad que los gerentes de planta deben conocer, pero es posible que no estén tan familiarizados como deberían.
El hecho de que el estándar de control de energía peligrosa de OSHA sobre bloqueo y etiquetado sea uno de los 10 estándares más citados, no asegura que los gerentes de planta estén considerando sus normativas en su totalidad.
Vale la pena señalar que la «energía peligrosa» no se limita a la energía eléctrica. Las normas también incluyen considerar: la energía mecánica, incluidos los resortes, la hidráulica, entre otros.
Un concepto erróneo es pensar que un programa aislado de etiquetado es una sustitución aceptable al de un programa de bloqueo. Pero no es así, en algunos casos las etiquetas se pueden quitar fácilmente sin darse cuenta, lo que podría exponer a los trabajadores a peligros eléctricos graves.
Los tipos de hardware de bloqueo también son consideraciones importantes. Por ejemplo, los tipos de candados deben ser visualmente identificables según su propósito y deben de diferenciarse fácilmente de otros para evitar confusiones.
Otro error común, es considerar que un programa de bloqueo y etiquetado se compone de una colección de candados y etiquetas que se pueden utilizar para aislar el equipo de la energía. El hecho es que un programa de bloqueo y etiquetado también incluye una amplia documentación de los procesos y procedimientos que los trabajadores deben seguir para eliminar la energía peligrosa del equipo.
Seguridad de una instalación de procesamiento de alimentos
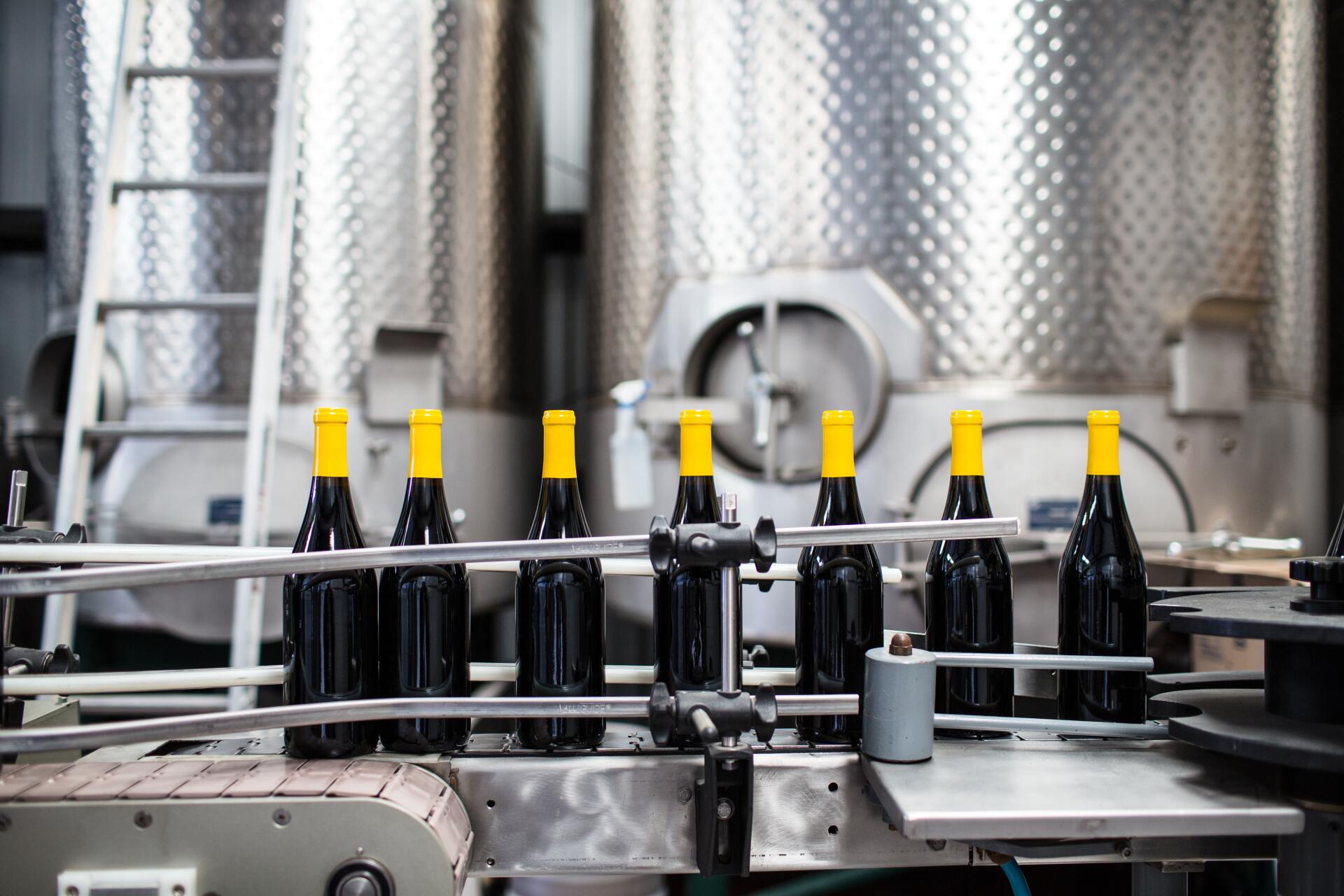
Así como en las plantas de procesamiento de alimentos existen diferentes niveles de higiene, también debe de contar con capacitación especializada a los diferentes tipos de empleados según sus actividades.
Esta capacitación permite mejorar la relación del empleado con las cualidades propias de una pieza o piezas de equipo o maquinaria, por lo que un programa de capacitación general es insuficiente.
El reentrenamiento no se basa necesariamente en el tiempo transcurrido a la última capacitación de personal. Tienen que tomarse en cuenta otros factores, como cuando se realizan cambios en el programa de Bloqueo y Etiquetado, la introducción de nuevos equipos, por rotación de personal o al descubrir que un empleado infringe los procedimientos establecidos.
Si se introducen nuevos tipos de arrancadores de motor manuales que están diseñados específicamente para aplicaciones especiales, su uso en la aplicación incorrecta puede crear un peligro para la seguridad. Por lo que sería necesario capacitación al respecto.
La actualización del personal, permite conocer las diversas subclases de arrancadores de motor manuales identificados como «adecuados para desconexión del motor». Esto significa que deben de familiarizarse con las diferentes modalidades, ya que estos se pueden utilizar tanto para el control de encendido y apagado como para satisfacer los requisitos de uso como interruptor de desconexión de seguridad.
Proteger la instalación de problemas eléctricos
Se requiere una protección adecuada contra cortocircuitos y sobrecargas para proteger contra daños al sistema eléctrico. Durante la instalación de nuevos equipos, una sobrecarga podría interrumpir el flujo de energía y dañar los equipos. Además, el mantenimiento inadecuado de un cableado o una herramienta fuera de lugar, podrían hacer que estos dispositivos limitadores de corriente se activen.
Existen protocolos a seguir para proteger al personal y las máquinas de descargas, prevenir incendios y otros eventos dañinos debido a la presencia de energía eléctrica o fallas eléctricas. Una descripción general de algunas de las muchas protecciones eléctricas incluye:
- Proporcionar un medio de desconexión bloqueable
- Puertas de interbloqueo para desconectar la energía
- Incluir etiquetas de seguridad
- Proporcionar protección contra sobrecorriente
- Proporcionar protección contra altas tensiones.
Este artículo es un primer paso en la discusión de seguridad eléctrica general. Es importante tener en cuenta que existen excepciones a muchos requisitos, así como normativas con especificaciones importantes que se abordarán en artículos posteriores.
Aunque a menudo se pasan por alto, las desconexiones automáticas en los sistemas de control industrial realizan la importante función de garantizar la protección del personal de mantenimiento y de la maquinaria.
Las regulaciones y normativas existentes exigen que se apague, bloquee y etiquete toda la energía del equipo. Si bien, una desconexión es la mejor forma de bloquear la alimentación eléctrica de un panel de control, también existen otros métodos que protegen al personal del contacto directo con voltajes peligrosos.